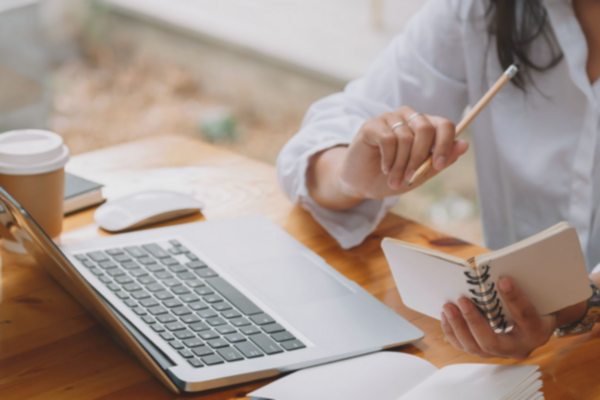
A Complete Learning and Reference Package for the Mining Industry! This bundle offers one-year access to Edumine Answers, the most comprehensive mining knowledge resource, and Introduction to Modern Mining, our flagship mining fundamentals course. Whether you're new to the industry or an industry veteran, this has got you covered. What’s Included? Edumine Answers Subscription – Our new interactive learning tool allows you to ask free-form questions and receive instant, accurate answers whenever and wherever you need them. The answers are drawn from our meticulously curated library of over 110 peer-reviewed courses, which are continuously updated to reflect the latest industry knowledge. Introduction to Modern Mining Course – A structured introduction to today’s mining industry, covering exploration, extraction, processing, sustainability, and investment. This course provides essential insights into modern mining practices and industry trends, making it the perfect starting point for industry newcomers. Who Is This For? Professionals and decision-makers who need quick, reliable mining insights Investors and analysts looking for expert-backed information on mining operations and markets Technical personnel such as geologists, chemists, engineers, data scientists, and procurement specialists seeking an accessible reference tool Students and newcomers wanting a structured introduction to modern mining Government officials, regulators, policy setters, and members of non-governmental organizations (NGOs). Equip yourself with one year of unlimited expert access and a strong industry foundation with the Edumine Fundamentals Bundle—your key to navigating the modern mining world with confidence! Why Edumine Answers? Watch the 1 Minute Demo Read more
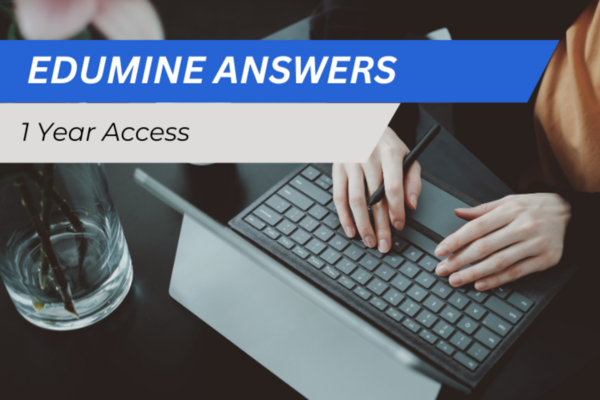
The Smartest Way to Learn in Mining! We are excited to announce that Edumine is now leveraging cutting-edge AI technology to enhance your learning experience! Our new interactive learning tool allows you to ask free-form questions and receive instant, accurate answers drawn from our meticulously curated library of over 110 peer-reviewed courses. Subscribe now and get 12 months of access! The first stop for learning and decision-making in a rapidly evolving industry, bridging the gap between experience and instant knowledge. Edumine Answers is an AI-powered mining knowledge tool that provides instant, expert-vetted answers to technical, operational, and strategic questions. Whether you’re an engineer, geoscientist, mine manager, HR professional, or investor, Edumine Answers delivers instant answers whenever and wherever you need them. Watch the 1 Minute Demo Read more
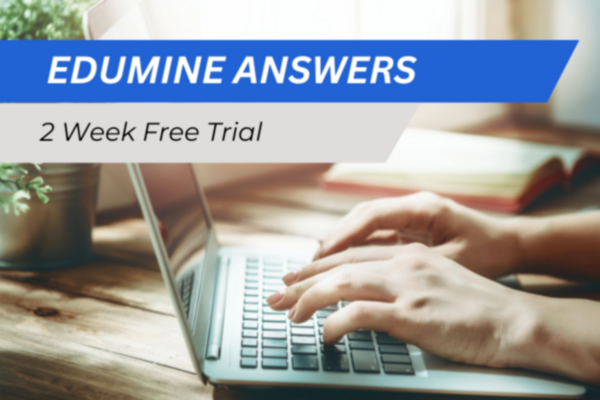
The Smartest Way to Learn in Mining! We are excited to announce that Edumine is now leveraging cutting-edge AI technology to enhance your learning experience! Our new interactive learning tool allows you to ask free-form questions and receive instant, accurate answers drawn from our meticulously curated library of over 110 peer-reviewed courses. Start your 2-week free trial and experience the knowledge you need to succeed. The first stop for learning and decision-making in a rapidly evolving industry, bridging the gap between experience and instant knowledge. Edumine Answers is an AI-powered mining knowledge tool that provides instant, expert-vetted answers to technical, operational, and strategic questions. Whether you’re an engineer, geoscientist, mine manager, HR professional, or investor, Edumine Answers delivers instant answers whenever and wherever you need them. Watch the 1 Minute Demo Read more
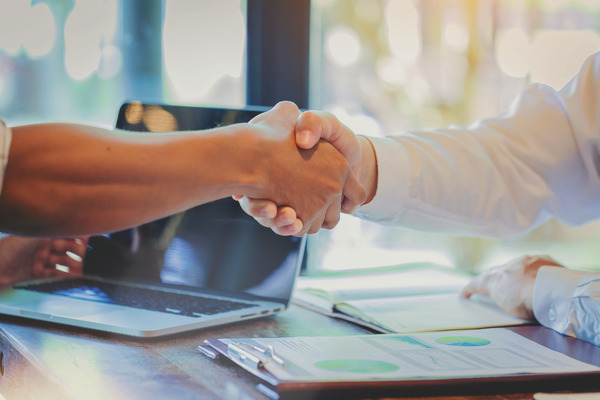
Master the Complexities of Mining Sales Unlock the strategies and skills you need to thrive in the unique and challenging world of mining sales. This course provides sales professionals with the tools to build lasting client relationships, tailor sales approaches to high-stakes mining deals, and effectively communicate value to industry decision-makers. Who is this course for? This course is designed for sales professionals new to the mining industry or those seeking to enhance their knowledge and approach to selling in this high-value, long-cycle sector. What you’ll learn Understand the Mining Sales Cycle: Gain insight into the extended timelines, high-value transactions, and multi-stakeholder dynamics that characterize mining sales. Tailored Sales Techniques: Apply sales methodologies designed for large-scale mining industry deals to close more efficiently. Build Lasting Client Relationships: Learn how to foster trust and secure repeat business with strong client connections. Communicate Value Effectively: Articulate value propositions that address technical, operational, and financial perspectives. Overcome Complex Sales Challenges: Navigate objections, handle group selling situations, and lead structured conversations that align with the buyer’s decision-making process. Take the first step toward mining sales success. Enroll today and transform your approach to selling in this niche industry. Author Adam Basheer Need to train a team? Whether you're looking for a customized training program or developing a team, we have enterprise solutions to fit your needs. Learn More Read more
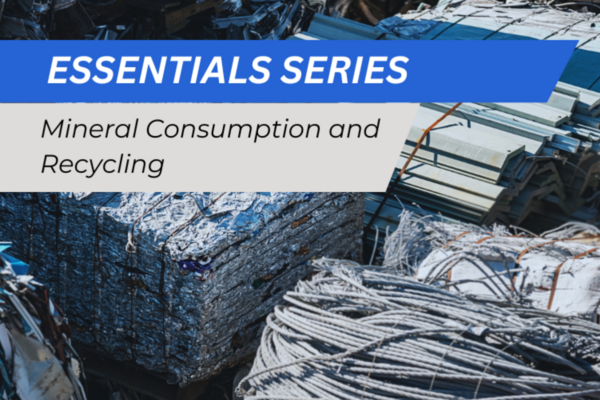
About the Course This course provides a non-technical introduction to the basic concepts of mineral consumption and recycling, with numerous examples, figures and images of mining. Explore the complex dynamics of mineral consumption, supply, demand, and recycling, and their implications on the mining industry and global resources. Explore sustainable mining practices and the role of small-scale miners in today’s global economy. Learn about recycling's impact as a complementary approach to mining, and its environmental and economic benefits. Explore the dynamics of recycling through concepts such as the "Law of Recycling", recycling rates, recovery rates, and the challenges in the recycling process. Learn about different metals, their recycling timelines, and the factors influencing effective recycling. Audience High school science Author Dr. Marcello Veiga Need to train a team? Whether you're looking for a customized training program or developing a team, we have enterprise solutions to fit your needs. Learn More Read more
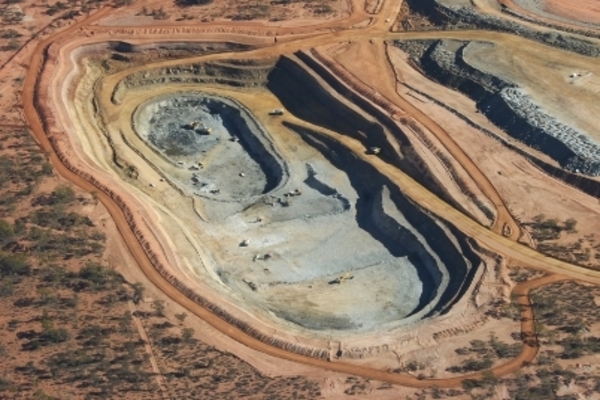
Este curso es el tercero de una serie de tres cursos sobre planificación minera y es la continuación de los dos cursos anteriores. Planificación minera 1: estrategia se centró en tres de las cinco palancas principales para la creación de valor como parte del proceso de planificación minera estratégica (incluida la selección del método de minería, la selección de la ruta del proceso y la escala de operación). Planificación minera 2: operaciones luego ilustró el uso de las dos palancas finales, incluidas la secuencia y la programación y la política de ley de corte. Planificación minera 3: optimización le presenta los conceptos de optimización matemática que a menudo forman la base de muchas de las herramientas de planificación computarizadas que están disponibles comercialmente en la actualidad. Es importante comprender cómo funcionan estas herramientas y los algoritmos fundamentales detrás de ellas para ayudar en el proceso de planificación minera. Alcance Este curso se centra en el uso de técnicas y procesos de optimización matemática. Al finalizar este curso, los participantes podrán desarrollar modelos básicos de programación matemática y resolverlos en Excel con el fin de asignar recursos limitados para obtener el máximo beneficio (dentro del contexto minero). La codificación y la creación de scripts están fuera del alcance de este curso. Autores Dr. Micah Nehring Ph.D. Dr. Sean Shafiee Ph.D. Duración: 20 horas Categoría: Minería Fecha de la versión: 21 de septiembre de 2017 Read more
Shopping Cart
Your cart is empty